Technical Insight
Bit Rock Interaction and Modelling
High Rates of Penetration (ROPs) with a good borehole stability in hard rock or heterogeneneous formations such as Chert, Conglomerates and Granite remains one of the major challenges in downhole drilling. To optimise the cutting process, a better understanding of the mechanics of force generation and its relationship with a number of key drilling parameters is needed. However, the intricacy of bit-rock interactions and the physics of formation fracture makes rock drilling a challenging task from an analytical and numerical modelling perspective.
In this context, a series of laboratory based projects were undertaken with the twin aims of unveiling the complexity of the dynamic interactions between the drill-bit and a drilled formation and to develop a model which could plausibly capture the mechanics of the process, and in particular be able to predict the cutting forces for various operating conditions.
In these projects, the contact fracturing of brittle materials with a cylindrical indenter was studied and a new fracturing mechanism was developed by focusing on contact stress and on the analysis of contact energy. This led to the determination of a contact crack initiation angle. The investigative work included a comprehensive experimental study as well as a finite element (FEM) analysis of the contact fracturing mechanism, as shown in the following schematic.
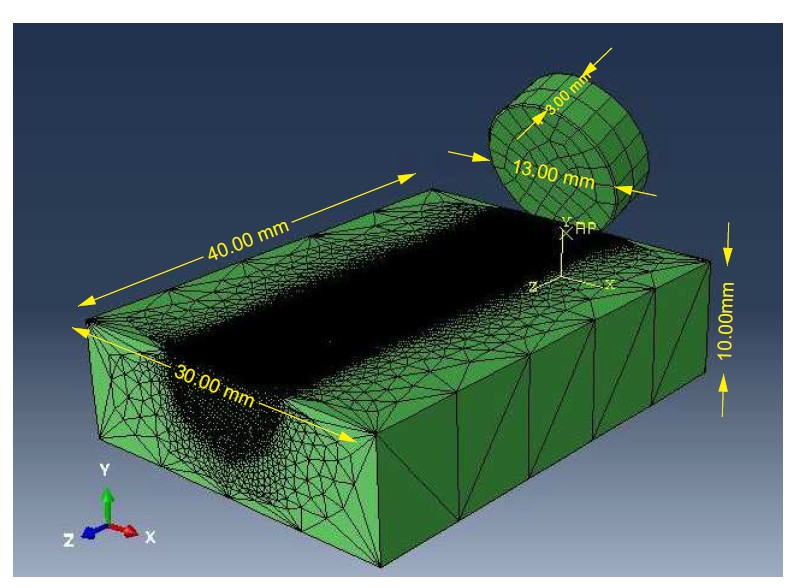
Figure 1 Geometry, size and mesh of the 3D FE model of rock cutting.
In a next stage of the project, extensive rock cutting experiments were performed with single PDC cutters, and this allowed us to investigate the effects of different operating parameters on PDC cutter response. Additionally, an analytical model for evaluating the rock cutting forces was proposed and incorporated into a FEM model of the rock cutting process. The results from both analytical and FEM models were deemed to be legitimate when compared to the experimental tests.
Lastly, the dynamic interactions between the rock and a PDC drill-bit in rotary drilling was investigated by carrying out an extensive programme of tests on PDC drill-bits. Moreover, a relation between the single cutter force response and the full PDC drill-bit was studied, and a conceptual hypothesis for the torque response of drill-bits was proposed.
To support these projects both to have experimental validations for our numerical models and to be able to examine innovative drill-bit designs, a new facility was established by the Centre for Applied Dynamics Research (CADR) and it hosts two rig set-ups to investigate drill-string dynamics and rock mechanics. Schematics of each of these two rigs are shown below.
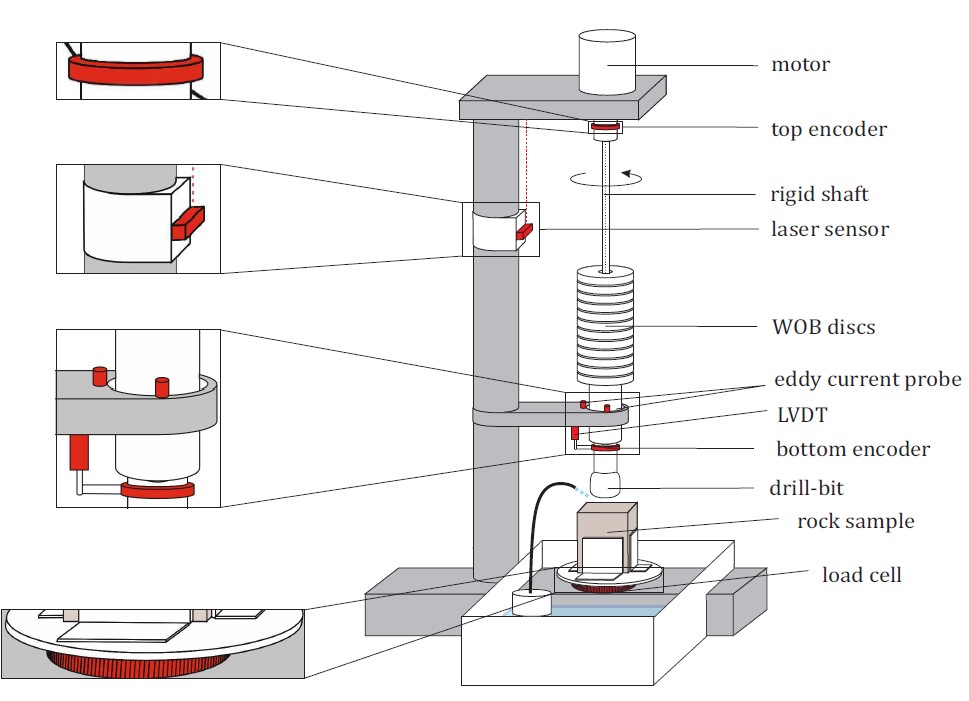
Figure 2 Schematic of the drill-string rig setup. The system includes an electric motor, drill-pipe, top and bottom encoder, discs, BHA, Laser displacement sensor, LVDT sensor, 4-component load cell, eddy current probes, drill-bit and holder, rock sample and rock.
The drill-string rig is unique worldwide as it is capable to study all nonlinear and dangerous phenomena during drilling rock samples; this is in contrast to other facilities which only simulate the resulting loads. The rig operates in two configurations of flexible and rigid shaft. It provides controllable rotational speed and Weight-on-Bit (WOB) for different rock samples and drill-bits, and allows for measurement of a range of parameters such as angular velocity of the top and bottom of the drill-string, lateral motion, Torque-on-Bit (TOB) and Rate-of-Penetration (ROP). The rig employs a LabView graphical interface for real-time response monitoring.
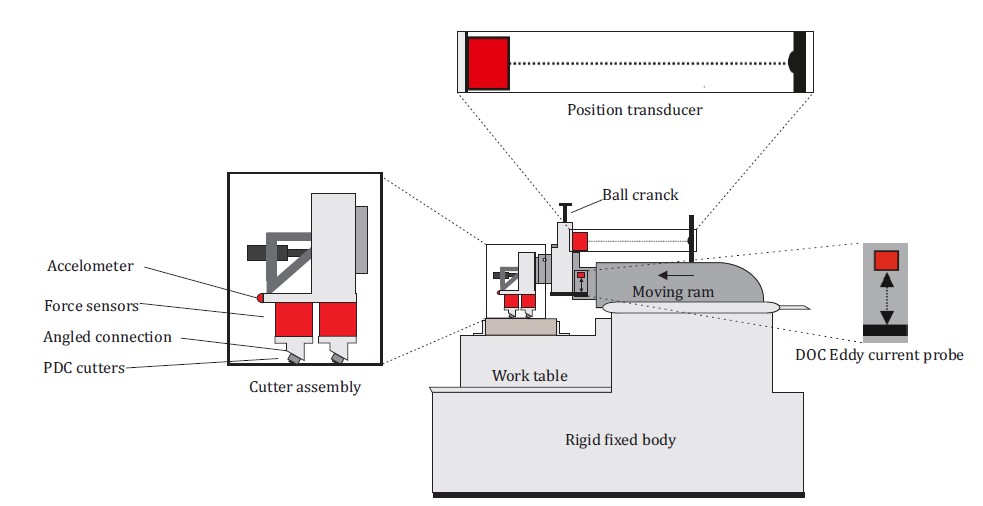
Figure 3 Schematic of single cutter rig with its main components: motor controller, displacement sensor (LVDT), accelerometer, 3D force sensor, DOC probe and PDC cutter assembly.
The rock mechanics work for the single cutter rig above is focused on studying the rock cutting forces, and are conducted on linear cutter rigs. This enabled us to gain a fundamental understanding of the interactions between a single cutter and the rock formation based on which we developed models to predict cutting conditions for the entire drill-bit. The single cutter is attached to a three-dimensional force sensor which can measure normal and horizontal cutting forces. The rig can be equipped with two cutter holders to allow for the investigation of two successive cutters on a drill-bit.
Reach Us
Please send an email to the addresses below or use the form to contact us.
Fraser Noble Building, School of Engineering, University of Aberdeen, Kings College Aberdeen AB24 3UE, Scotland, UK
+ 44 (0) 1224 274177