Technical Insight
Whirling of Bottom Hole Assemblies and Rotors
Here we provide some technical insights from the analysis of the nonlinear dynamic whirling behaviour of Bottom Hole Assemblies (BHAs) in well drilling and of rotors within rotation machinery.
At the very core of iVDynamics research and development is the application of the most advanced modelling and analysis methods from the area of nonlinear dynamics, which offers superior tools supporting engineering design. Some projects require fundamental studies which are undertaken by iVDynamics in collaboration with the Centre for Applied Dynamics Research (CADR) at the University of Aberdeen. For the last 15 years, CADR has been a world leading group in the area of nonlinear dynamics and in its application to various branches of engineering with a focus on the energy industry.
At iVDynamics, and with the support of CADR, we develop advanced nonlinear dynamic models that are calibrated by rigorous experiments and that can accurately predict the onset and severity of nonlinear phenomena, which can be either harvested or avoided. Such models enable us to design efficient and safe solutions that take full advantage of the system dynamics.
A particular application of this capability relates to the nonlinear whirling motions observed both in drilling BHAs and in the bearing clearance of rotors within rotating machinery, as shown in the two schematics below.
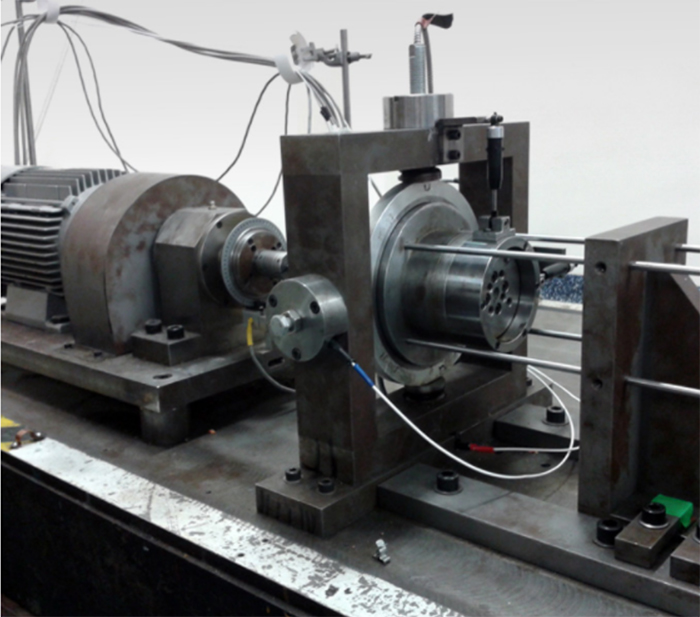
Rotor Rig for Experimental Verification of an Asymmetric Jeffcott Rotor
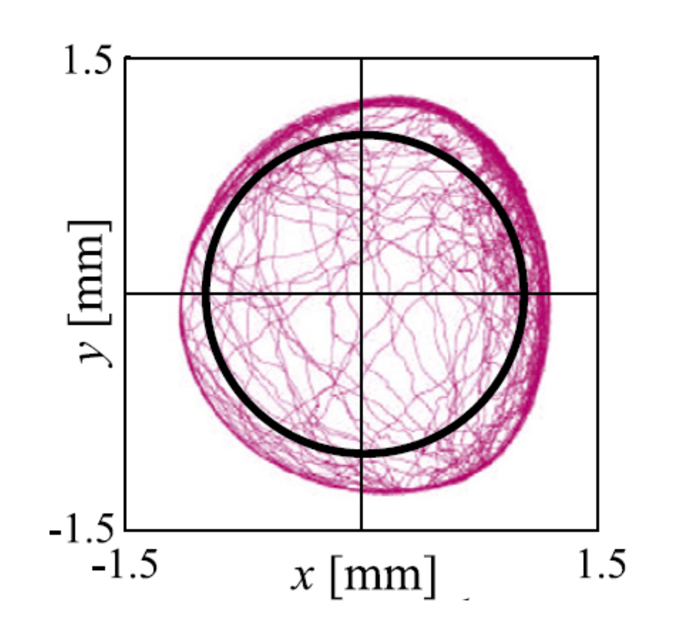
Whirling of rotors and BHAs.
CADR has been investigating whirling phenomena in rotors and Bottom Hole Assemblies (BHAs) for over 20 years with support from both industry and government. A first initiative started in early 2000 on a joint industry project with Rolls-Royce on the dynamics and control of rotor systems within rotating machinery using Smart Memory Alloys (SMAs). The project was co-funded by the Engineering and Physical Research Council (EPRSC).
The first aim of this study was to develop robust models describing the mechanical behaviour of these SMAs in terms of induced stress and temperature, as shown on the panels (a) and (b), respectively, of Figure 1.
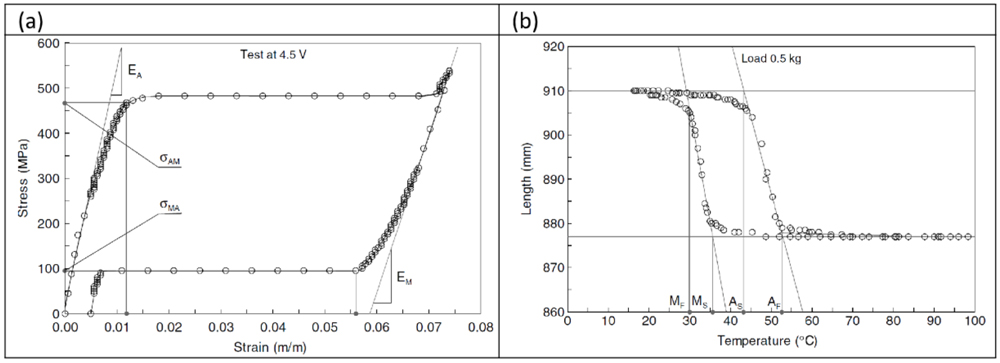
Figure 1. Mechanical characteristics of Flexinol actuator wire [1] showing (a) loading and unloading curves (b) changes of length as a function of ambient temperature.
The second aim of the study was to design and investigate SMA based support structures which are used to alter the dynamical properties of rotor systems often exhibiting strongly nonlinear responses. One particular focus of this study was to examine a bearing clearance in the rotor system and the effects of such a clearance on the global dynamics of the rotor. Figure 2 presents an experimental rig shown in panel (a) and a low dimensional numerical model depicted in panel (b) of the rotor system with a bearing clearance [2]. This rotor system has been extensively investigated theoretically and experimentally [3] showing a very rich dynamical behaviour and an excellent match between theory and experiment, as shown in the bifurcation diagrams of Figure 3.
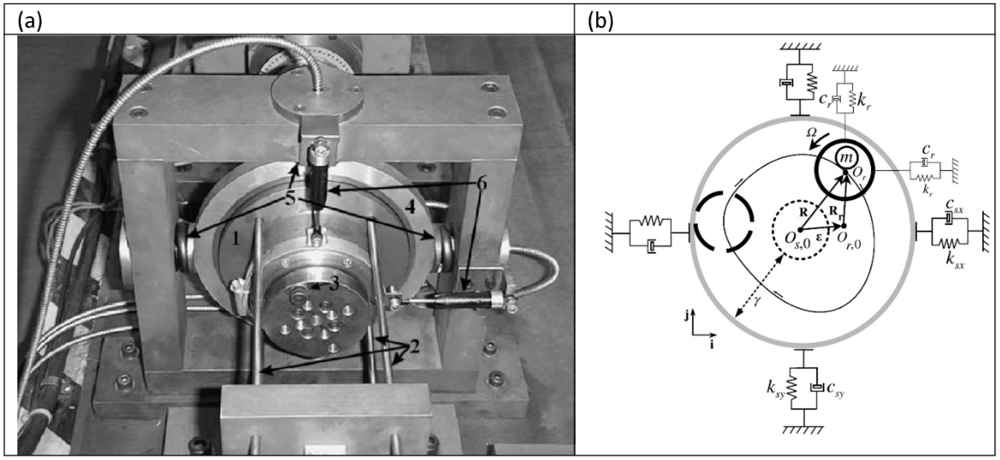
Figure 2. (a) Experimental rig of the Jeffcott rotor with a preloaded snubber ring and (b) its low dimensional physical model.
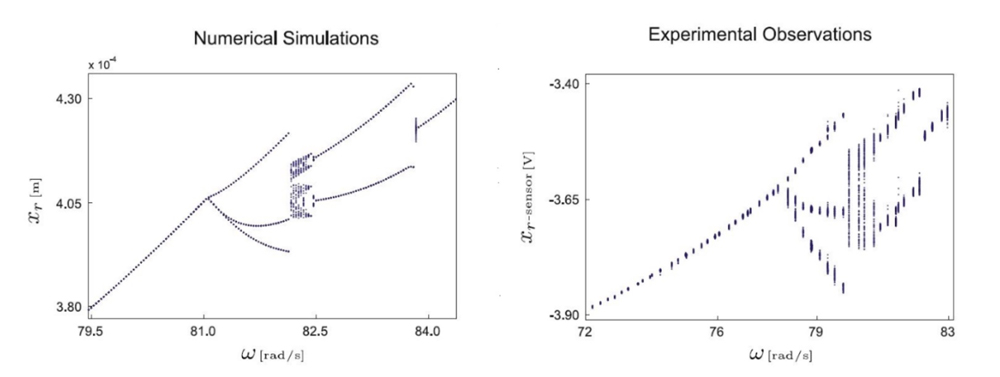
Figure 3. Comparison of the bifurcation diagrams obtained from mathematical modelling (left-hand side panel) and experimentally (right-hand side panel).
Very similar dynamical behaviour has been seen for whirling BHAs and drill-strings which is being caused by the interactions with the borehole and / or the stabilisers. Whirling of a BHA and its drill-string is considered to be an undesirable response that can result in serious or even catastrophic damage.
There are two types of whirls, forward and backward, where the BHA whirls in the same and opposite direction as the drill-bit, respectively. The latter one, the backward whirl is associated with much intensive dynamic interaction and can be dangerous for the BHA. Our recent theoretical and experimental studies [4] suggest that these two types of whirls co-exist, as is shown in Figure 4 below.

Figure 4. A map showing different types of possible co-existing whirling solutions depending on different initial conditions, where red, blue and grey colours represent periodic forward, periodic backward and chaotic forward whirl, respectively.
References
- Zak, A.J., Cartmell, M.P., Ostachowicz, W.M. and Wiercigroch, M., 2003. One-dimensional shape memory alloy models for use with reinforced composite structures. Smart Materials and Structures, 12(3), p.338. (https://abdn.pure.elsevier.com/en/publications/one-dimensional-sma-models-for-use-with-reinforced-composite-stru)
- Karpenko, E.V., Pavlovskaia, E.E. and Wiercigroch, M., 2003. Bifurcation analysis of a preloaded Jeffcott rotor. Chaos, Solitons & Fractals, 15(2), pp.407-416. (https://abdn.pure.elsevier.com/en/publications/bifurcation-analysis-of-a-preloaded-jeffcott-rotor)
- Chávez, J.P., Vaziri, V. and Wiercigroch, M., 2015. Modelling and experimental verification of an asymmetric Jeffcott rotor with radial clearance. Journal of Sound and Vibration, 334, pp.86-97. (https://abdn.pure.elsevier.com/en/publications/modelling-and-experimental-verification-of-an-asymmetric-jeffcott)
- Kapitaniak, M., Vaziri, V., Chávez, J.P. and Wiercigroch, M., 2018. Experimental studies of forward and backward whirls of drill-string. Mechanical Systems and Signal Processing, 100, pp.454-465. (https://abdn.pure.elsevier.com/en/publications/experimental-studies-of-forward-and-backward-whirls-of-drill-stri)
Reach Us
Please send an email to the addresses below or use the form to contact us.
Fraser Noble Building, School of Engineering, University of Aberdeen, Kings College Aberdeen AB24 3UE, Scotland, UK
+ 44 (0) 1224 274177